IFOY Patronage
IFOY Sponsor
Jungheinrich & MHP @ Wildeboer
Jungheinrich
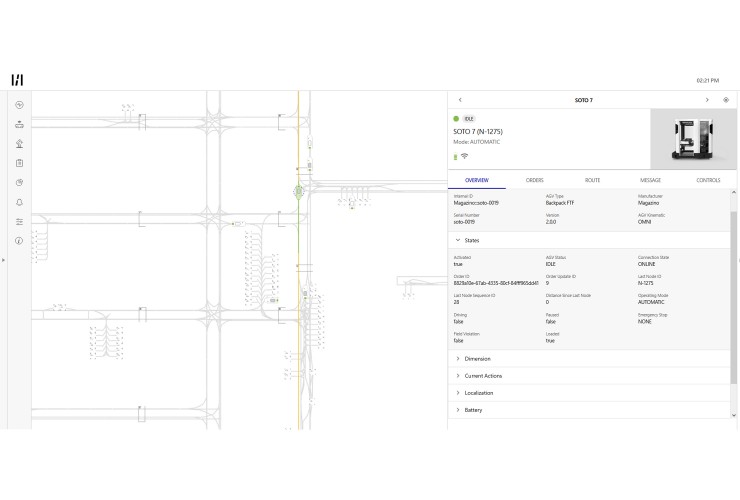
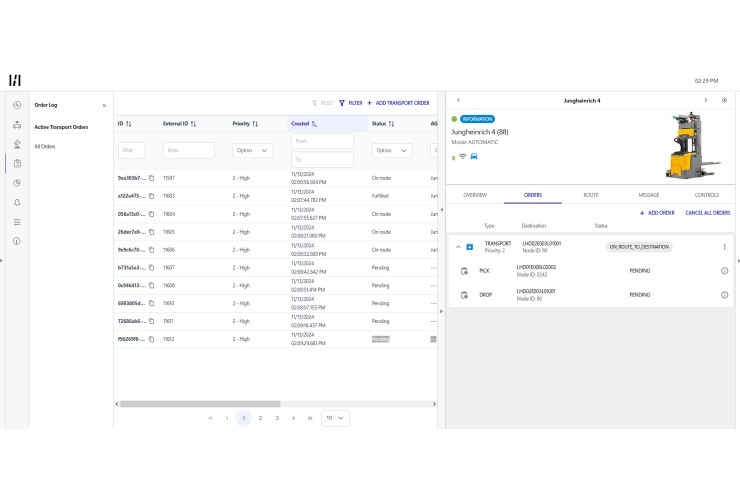
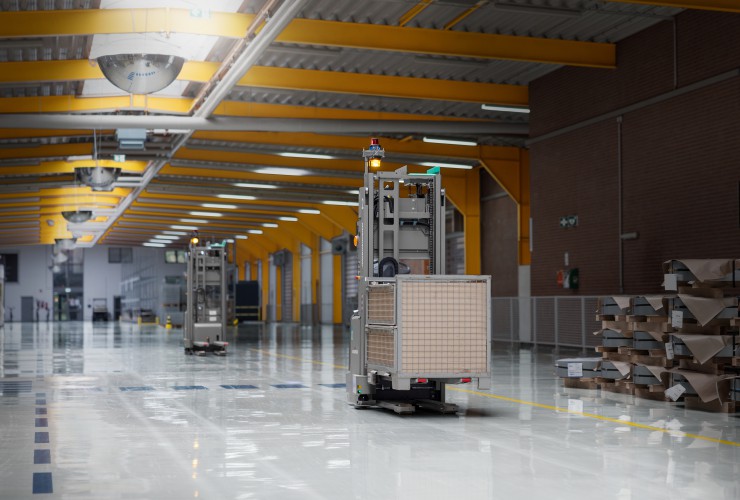
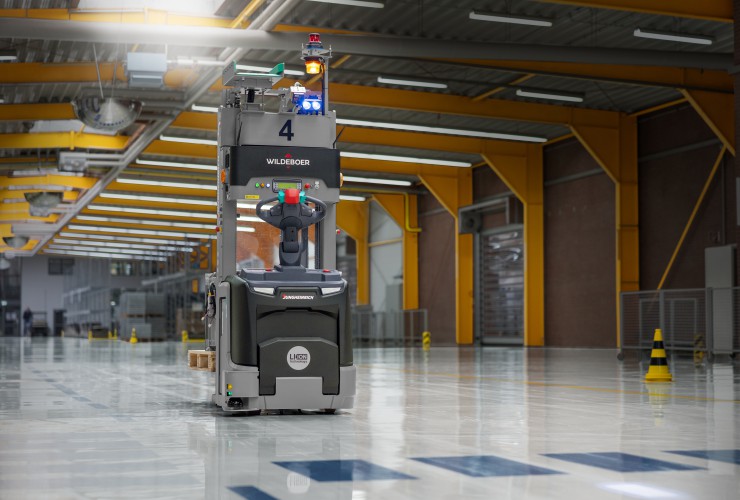
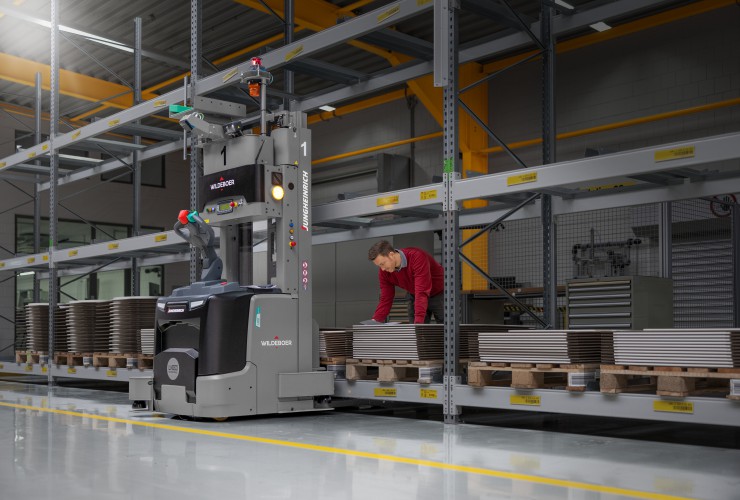
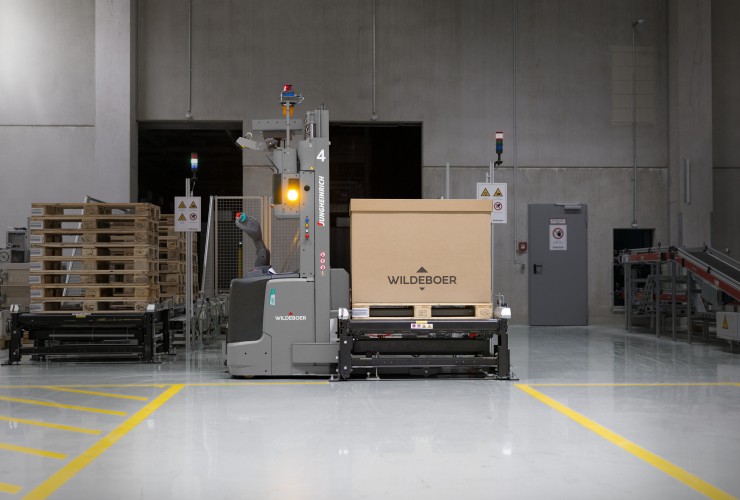
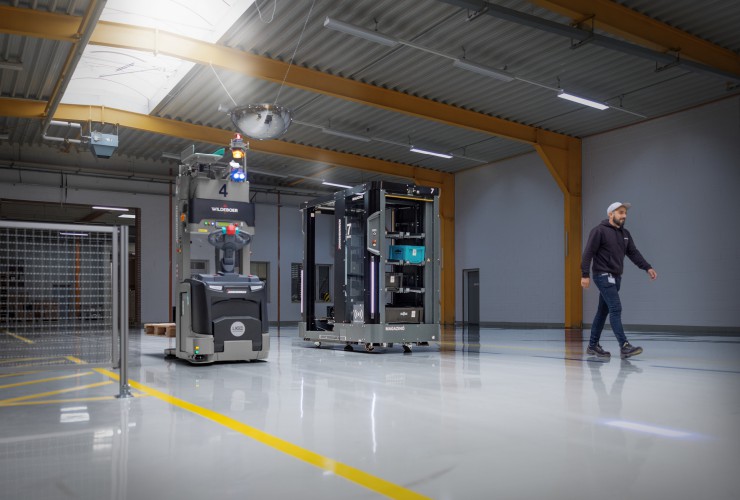
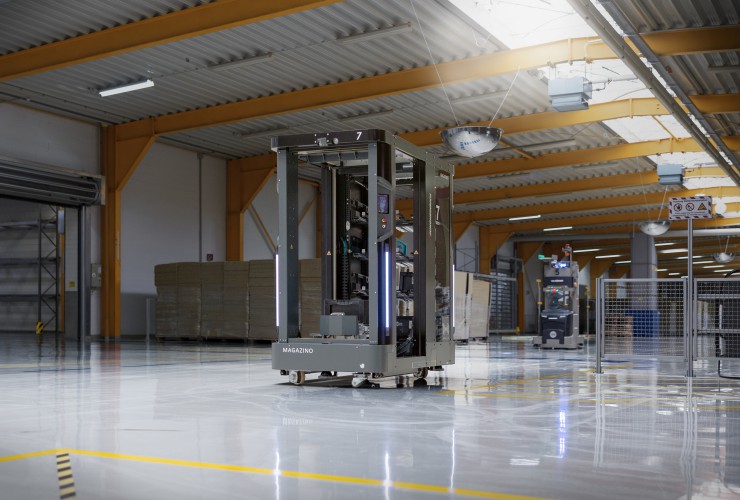
IFOY-Kategorie
Integrated Customer Solution
Zusammenfassung
Der Bau eines neuen Logistikzentrums hatte das Ziel, die Lagerkapazitäten zu erweitern und die Durchlaufzeiten zu verkürzen. Für die Automatisierung der innerbetrieblichen „letzten Meile“ vom Logistikzentrum in die Produktion setzt die Wildeboer Bauteile GmbH Mobile Robots von Jungheinrich in Kombination mit einem herstellerunabhängigen Flottenmanagementsystem von MHP ein. Das Highlight: Der gleichzeitige Betrieb verschiedener Mobile Robots gesteuert von einem externen VDA 5050-Flottenmanager.
Kunde
Wildeboer Bauteile GmbH
Umsetzungszeitraum
Von: 02.10.2023
Bis: 20.12.2024
Investitionsvolumen
1.198.850,00€
Bewerbungsdaten
Case Study
Die Wildeboer Bauteile GmbH aus Weener entwickelt, produziert und vertreibt Komponenten für Brandschutz, Luftverteilung, Gebäudesystemtechnik und Schallschutz. Ob Bürogebäude, Shoppingmall, Hotel, Gesundheitswesen oder Events – die Bauteile von Wildeboer kommen in vielfältigen Branchen zum Einsatz. Zur Erweiterung der Lagerkapazität und Optimierung der Prozesszeiten realisierte Wildeboer in Zusammenarbeit mit Jungheinrich eine zukunftsfähige Automatisierungslösung in einem neu errichteten Logistikzentrum.
Für den Transport von Ladungsträgern vom Automatiklager in die Produktion und von Produktionsschritt zu Produktionsschritt sowie für den Rücktransport wurde eine Automatisierungslösung mit Mobile Robots installiert. Sechs Mobile Robots ERC 213a übernehmen den Transport von Großladungsträgern (GLT) bestehend aus Europaletten und Gitterboxen, während der autonome Mobile Robot SOTO für den Transport von Kleinladungsträgern (KLT) zuständig ist. Gesteuert wird das Zusammenspiel der Mobile Robotes durch eine herstellerunabhängige Software, dem MHP-FleetExecuter. Das Jungheinrich Logistics Interface fungiert als Middle Layer zwischen dem MHP-FleetExecuter und der Peripherie, bestehend aus Fördertechnik, Schnelllauftoren und einer Brandmeldezentrale.
Mit den Jungheinrich ERC 213a wurden bewährte Mobile Robots zur Automatisierung wiederkehrender Transportaufgaben auf engstem Raum eingesetzt. Dank ihres kompakten Designs eignen sie sich optimal für geringe Arbeitsgangbreiten. Neben hoher Prozesssicherheit und kurzer Amortisationszeit überzeugen sie durch ihre effiziente Antriebstechnologie mit nachhaltiger Lithium-Ionen-Batterie, sowie umfangreiche Sicherheitssysteme für den reibungslosen Einsatz im Mischbetrieb.
Der SOTO eignet sich hervorragend für den automatisierten Transport von Kleinladungsträgern entlang der Produktionslinie sowie für die Ein- und Auslagerung direkt in und aus Durchlaufregalen oder auf Förderbänder. Er ermöglicht die Materialverfolgung in Echtzeit und bietet so maximale Prozesssicherheit. SOTO nimmt bis zu 14 KLT in zwei verschiedenen Größen problemlos von zwei Seiten auf und transportiert sie sicher an ihren Bestimmungsort. Sein verstellbarer Greifer erreicht Höhen zwischen 400 und 1.700 mm und ermöglicht eine 180 Grad-Drehung der KLT – für ein präzises und stufenloses Handling in unterschiedlichen Regalhöhen. Vier Laserscanner und zwei 3D-Kameras sorgen für ein hohes Maß an Sicherheit im Umgang zwischen Mensch und Maschine.
Automatisiertes Handling auf einem neuen Effizienzniveau
Im automatischen Hochregallager und dem automatischen Kleinteillager (AKL) von Wildeboer werden die kommissionierten Aufträge auf Ladungsträgern in Form von Großladungsträgern (GLT) und Kleinladungsträgern (KLT) für den Transport in die Produktion vorbereitet. Die Zuteilung der Transportaufträge zum jeweils passenden und optimal positionierten Fahrzeug erfolgt durch den MHP-FleetExecuter. Hierbei wird bei SOTO-Transporten zusätzlich eine Tourenbildung auf Basis kürzester Zwischenstrecken durchgeführt, um eine effiziente Gesamtfahrt zu gewährleisten. Anschließend werden die Aufträge per VDA 5050-Schnittstelle an den mobilen Roboter SOTO und die ERC 213a übertragen, die diese wiederum ausführen und Rückmeldungen liefern. So schafft der Kunde mehr als 83 Paletten- und Gitterboxtransporte pro Stunde und erhöht durch den SOTO spürbar die Geschwindigkeit und Effizienz der KLT-Transporte mit 22 KLT pro Stunde.
Neuartig bei dieser Automatisierungslösung ist die Kombination von verschiedenen Mobile Robots innerhalb eines Logistiksystems unter der zentralen, herstellerunabhängigen Leitsteuerung eines externen Flottenmanagementsystems. Die besondere Herausforderung bei der Umsetzung der Automatisierungslösung bestand neben der Tourenplanung und dem Backpack-Management des SOTO über den VDA 5050-Leitrechner darin, den Betrieb der unterschiedlichen Flurförderzeuge, die nicht zwingend von einem Hersteller stammen müssen, aufeinander abzustimmen und einen effizienten Warenfluss mit allen Komponenten zu gewährleisten. Die Forderung nach einem zukunftsfähigen System, das die kurzfristige Einbindung weiterer Fahrzeuge und Lieferanten ermöglicht, wurde erfolgreich umgesetzt.
Skalierbar und zukunftsfähig
Als Generalunternehmer und fester Ansprechpartner für Wildeboer im gesamten Projektverlauf lieferte Jungheinrich eine Automatisierungslösung, die mit ihren Aufgaben wächst und dem Kunden maximale Flexibilität bietet. Auf Veränderungen in der Intralogistik kann zukünftig durch die kurzfristige Integration neuer Robotertypen wie zum Beispiel Schwerlast-AGV oder Reinigungsmaschinen per standardisierter VDA 5050-Schnittstelle reagiert werden. Im ersten Schritt wurden zunächst sechs ERC 213a-Fahrzeuge und ein SOTO installiert. Sollte sich das Transportaufkommen durch eine andere Taktung in der Produktion erhöhen, können problemlos weitere Fahrzeuge hinzugefügt werden.
Durch die Automatisierung wiederkehrender Transportaufgaben konnte auch dem zunehmenden Fachkräftemangel entgegengewirkt werden. Seit Inbetriebnahme der Automatisierungslösung profitiert Wildeboer von einer signifikanten Steigerung der Produktivität, während die Mitarbeitenden durch die automatisierten Kollegen bei der Ausführung ihrer Tätigkeiten entlastet werden.
Fazit
Die große Herausforderung, mehrere Mobile Robots unter einem Dach mit Hilfe einer externen Schnittstellenlösung effizient zu betreiben, wurde im Projekt Wildeboer mit Bravour gemeistert. Jungheinrich liefert eine offene und flexible Automatisierungslösung, die dem Kunden die Freiheit bietet, je nach Aufgabenstellung und Bedarf externe Komponenten und Lieferanten in das System einzubinden.
IFOY Innovation Check
IFOY Innovation Check
Funktionalität / Art der Umsetzung
Die implementierte Automatisierungslösung bei der Wildeboer Bauteile GmbH gewährleistet die effiziente und zuverlässige Transportabwicklung innerhalb des neu errichteten Logistikzentrums. Die Funktionalität dieser Lösung basiert auf dem Einsatz verschiedener fahrerloser Transportfahrzeuge (FTF) für den innerbetrieblichen Materialfluss, sowohl im Bereich der Ladungsträger im Format von Paletten als auch bei den Kleinladungsträgern. Sechs Jungheinrich ERC 213a übernehmen die automatische Beförderung von Paletten zwischen Lager, Produktion und Rückführstationen. Parallel dazu ist der autonome Mobile Robot SOTO für die präzise Handhabung und den Transport von Kleinladungsträgern entlang der Produktionslinie verantwortlich. Die Steuerung der gesamten FTF-Flotte erfolgt durch die herstellerunabhängige Software MHP-FleetExecuter. Diese übernimmt nicht nur die intelligente Zuteilung der Transportaufträge auf die optimal positionierten Fahrzeuge, sondern führt bei den Transporten für Kleinladungsträgern zusätzlich eine Tourenoptimierung durch. Über die VDA 5050-Schnittstelle kommuniziert die Software effizient mit den eingesetzten FTF und sorgt für nahtlose Integration mit der umgebenden Fördertechnik. Durch den Einsatz dieser Technologie konnte Wildeboer eine signifikante Steigerung der Transportkapazität erzielen – mit über 83 GLT- und 22 KLT-Transporten pro Stunde – bei gleichzeitig gesteigerter Prozesssicherheit und reduziertem manuellen Aufwand.
Neuheit / Innovation
Die Kombination von SOTO für Kleinladungsträger und ERC 213a für Großladungsträger auf einem gemeinsam genutzten Transportlayout stellt eine zukunftsweisende Lösung dar. Durch die Umsetzung anspruchsvoller Funktionen wie der Tourenplanung und dem sogenannten Backpack-Management des SOTO wurde ein hoher Automatisierungsgrad bei gleichzeitig flexibler Skalierbarkeit erreicht. Die Fähigkeit, weitere FTF und sogar neue Hersteller ohne strukturelle Eingriffe in die Systemarchitektur einzubinden, stellt einen wesentlichen Innovationsschritt in Richtung modularer und erweiterbarer Intralogistiklösungen dar. In dieser Form ist es eine Neuheit in der Umsetzung, da bisher das Management gemischter Flotten nur aus Lösungen für sehr große Systeme bekannt war, wie sie in Werken der Automobilindustrie zu finden sind.
Kundennutzen
Für Wildeboer ergibt sich ein erheblicher Mehrwert durch die Implementierung einer gemischten Flotte aus Paletten- und Behälter-FTF, die zentral über ein leistungsfähiges, herstellerunabhängiges Flottenmanagementsystem gesteuert wird. Besonders relevant ist die zuverlässige Koordination aller Fahrzeuge auf gemeinsamen Verkehrsflächen – ermöglicht durch die VDA 5050-Schnittstelle. Dies steigert nicht nur die Prozesssicherheit, sondern reduziert auch den personellen Aufwand im innerbetrieblichen Materialfluss deutlich. Zudem ermöglicht die Lösung eine flexible Skalierbarkeit bei zukünftigen Erweiterungen. Damit profitiert Wildeboer von einer modernen, kosteneffizienten Automatisierung, wie sie bislang meist nur Großunternehmen vorbehalten war.
Marktrelevanz
Die vorgestellte Lösung hat eine sehr hohe Marktrelevanz, insbesondere für den industriellen Mittelstand, der gerade in Deutschland sehr ausgeprägt ist. Mit ihrer adaptiven, skalierbaren Struktur adressiert die Lösung die Anforderungen kleiner und mittlerer Unternehmen (KMU), die zunehmend nach automatisierten Logistiklösungen suchen, ohne über die Ressourcen großer OEMs zu verfügen. Die erfolgreiche Umsetzung bei Wildeboer dient als richtungsweisendes Beispiel dafür, wie selbst in Betrieben mit wenigen hundert Mitarbeitenden eine komplexe FTF-Flotte wirtschaftlich und effizient betrieben werden kann. Gerade im Hinblick auf den zunehmenden Fachkräftemangel und den Bedarf an flexiblen Produktions- und Logistikprozessen bietet dieses System einen zukunftsfähigen Ansatz mit hohem Verbreitungspotenzial.
IFOY Fazit
Die Unternehmen Jungheinrich und MHP haben für Wildeboer eine beeindruckende Funktionalität in einem sehr großen Layout umgesetzt. Der Kundennutzen resultiert insbesondere aus dem gewählten Transportmanagementsystem, das die Fahrzeuge der gemischten Flotte von Behälter- und Paletten-AGVs auf den gemeinsamen Verkehrsflächen über die VDA5050-Schnittstelle zuverlässig koordiniert. Diese Innovation war lange Zeit den großen Fahrzeugflotten der OEMs in der Automobilindustrie vorbehalten. Somit ist sie ein gutes Beispiel für eine Flotte aus Flurförderzeug in Unternehmen mit nur wenigen hundert Mitarbeitern. Gerade im deutschen Markt mit seinen vielen KMU hat diese Lösung eine sehr große Marktrelevanz.
Funktionalität / Art der Umsetzung |
++ |
Neuheit / Innovation |
+ |
Kundennutzen |
++ |
Marktrelevanz |
++ |
++ sehr gut / + gut / Ø ausgeglichen / - weniger / -- nicht vorhanden |
Jungheinrich & MHP @ Wildeboer
Jungheinrich
IFOY category
Integrated Customer Solution
Summary
The construction of a new logistics centre was aimed at expanding storage capacity and reducing throughput times. To automate the internal ‘last mile’ from the logistics centre to the production line, Wildeboer Bauteile GmbH uses mobile robots from Jungheinrich in combination with a manufacturer-independent software from MHP. The highlight: the simultaneous operation of different mobile robots controlled by an external VDA 5050 fleet manager.
Customer
Wildeboer Bauteile GmbH
Realisation Phase
From: 2023-10-02
To: 2024-12-20
Investment
1.198.850,00€
Entry Data
Case Study
Wildeboer Bauteile GmbH, based in Weener, develops, produces and distributes components for fire protection, air distribution, building system technology and sound insulation. Whether office buildings, shopping malls, hotels, healthcare facilities or events – Wildeboer components are used in a wide range of industries.
To expand its storage capacity and optimise process times, Wildeboer worked with Jungheinrich to implement a future-proof automation solution in a newly constructed logistics centre. An automation solution with mobile robots was installed to transport load carriers from the automatic warehouse to production and from one production step to production step, as well as for the return transport. Six ERC 213a mobile robots handle the transport of large load carriers (LLC) consisting of Euro plates and mesh boxes, while the autonomous mobile robot SOTO is responsible for transporting small load carriers (SLC). The interaction of the mobile robots is controlled by a manufacturer-independent software, the MHP-FleetExecuter. The Jungheinrich Logistics Interface acts as a middle layer between the MHP-FleetExecuter and the peripherals, consisting of conveyor technology, high-speed doors and a central fire alarm system.
With the Jungheinrich ERC 213a, proven mobile robots have been used to automate recurring transport tasks in confined spaces. Thanks to their compact design, they are ideally suited for narrow aisles. In addition to high process reliability and a short amortisation period, they impress with their efficient drive technology with a sustainable lithium-ion battery, as well as extensive safety systems for smooth use in mixed operation.
SOTO is ideal for the automated transport of small load carriers along the production line, as well as for storage and retrieval directly into and out of flow racks or onto conveyor belts. It enables real-time material tracking, thus providing maximum process reliability. SOTO can easily pick up 14 SLC in two different sizes from two sides and transport them safely to their destination. Its adjustable gripper can reach heights between 400 and 1,700 mm and allows the SLC to be rotated 180 degrees – for precise and infinitely variable handling at different rack heights. Four laser scanners and two 3D cameras ensure a high level of safety for people working in the vicinity of the machine.
Automated handling at a new level of efficiency
In the automatic high-bay warehouse and the automatic small parts warehouse at Wildeboer, the picked orders are prepared for transport to production on load carriers in the form of large load carriers (LLC) and small load carriers (SLC). The MHP-FleetExecutor allocates the transport orders to the appropriate and optimally positioned vehicle. In the case of SOTO transports, a route is also created based on the shortest intermediate distances to ensure an efficient overall journey. The orders are then transmitted via a VDA 5050 interface to the mobile robot SOTO and the ERC 213a, which in turn execute them and provide feedback. This enables the customer to handle more than 83 pallet and mesh box transports per hour and, thanks to the SOTO, to significantly increase the speed and efficiency of SLC transports with 22 SLC per hour.
What is new about this automation solution is the combination of different mobile robots within a logistics system under the central, manufacturer-independent control of an external fleet management system. The particular challenge in implementing the automation solution, in addition to the route planning and the backpack management of the SOTO via the VDA 5050 host computer, was to coordinate the operation of the different types of industrial trucks, which do not necessarily have to come from the same manufacturer, and to ensure an efficient flow of goods with all components. The requirement for a future-proof system that enables the short-term integration of additional vehicles and suppliers has been successfully realised.
Scalable and future-proof
As general contractor and permanent contact partner for Wildeboer throughout the entire project, Jungheinrich delivered an automation solution that grows with its tasks and offers the customer maximum flexibility. In future, it will be possible to respond to changes in intralogistics by integrating new robot types such as heavy-duty AGVs or cleaning machines at short notice via a standardised VDA 5050 interface. In the first step, six ERC 213a vehicles and a SOTO were installed. If the transport volume increases due to a different production cycle, additional vehicles can easily be added.
The automation of recurring transport tasks has also made it possible to counteract the increasing shortage of skilled labour. Since the automated solution was implemented, Wildeboer has benefited from a significant increase in productivity, while employees have been relieved of the burden of carrying out their tasks by their automated colleagues.
Conclusion
The major challenge of efficiently operating several mobile robots under one roof with the help of an external interface solution was mastered with flying colours in the Wildeboer project. Jungheinrich provides an open and flexible automation solution that offers the customer the freedom to integrate external components and suppliers into the system depending on the task and requirements.
IFOY Innovation Check
IFOY Innovation Check
Functionality / Type of implementation
The automation solution implemented at Wildeboer Bauteile GmbH ensures efficient and reliable transport handling within the newly constructed logistics center. This solution relies on various automated guided vehicles (AGVs) to manage internal material flows, handling both pallet-sized load carriers and small load carriers. Six Jungheinrich ERC 213a AGVs autonomously transport pallets between the warehouse, production, and return stations, while the autonomous mobile robot SOTO precisely handles and transports small load carriers along the production line. The manufacturer-independent software MHP-FleetExecuter centrally controls the entire AGV fleet. It not only intelligently assigns transport orders to the optimally positioned vehicles but also optimizes routes for small load carrier transport. The software efficiently communicates with the deployed AGVs via the VDA 5050 interface, ensuring seamless integration with the surrounding conveyor system. By leveraging this technology, Wildeboer has significantly increased transport capacity – handling over 83 GLT and 22 KLT transports per hour – while simultaneously enhancing process reliability and reducing manual effort.
Novelty / Innovation
The combination of SOTO for small load carriers and ERC 213a for large load carriers within a shared transport layout represents a forward-thinking solution. The implementation of advanced functions such as route planning and SOTO’s so-called backpack management has enabled a high degree of automation while maintaining flexible scalability. A key innovation lies in the ability to integrate additional AGVs, including models from different manufacturers, without requiring structural modifications to the system architecture. This modular and expandable approach marks a significant advancement in intralogistics. Previously, managing mixed AGV fleets at this level was primarily seen in large-scale systems, such as those used in the automotive industry.
Customer benefit
For Wildeboer, the implementation of a mixed fleet of pallet and container AGVs – centrally controlled by a powerful, manufacturer-independent fleet management system – delivers substantial added value. The ability to reliably coordinate all vehicles within shared traffic areas is particularly crucial and is enabled by the VDA 5050 interface. This not only increases process reliability but also significantly reduces the personnel required for internal material flow. Additionally, the solution allows for flexible scalability, supporting future expansions. As a result, Wildeboer benefits from modern, cost-efficient automation, a level of sophistication that was previously reserved for large enterprises.
Market relevance
This solution holds strong market relevance, particularly for industrial SMEs, which are prevalent in Germany. With its adaptive, scalable structure, the system is designed to meet the needs of small and medium-sized enterprises (SMEs) that are increasingly seeking automated logistics solutions but lack the extensive resources of large OEMs. The successful implementation at Wildeboer serves as a pioneering example of how a complex AGV fleet can be operated economically and efficiently even in mid-sized companies. Given the growing shortage of skilled workers and the increasing demand for flexible production and logistics processes, this system presents a future-proof approach with very high potential for widespread adoption.
IFOY verdict
Jungheinrich and MHP have implemented an impressive automation system in a large-scale layout for Wildeboer. The customer benefits particularly from the selected transport management system, which reliably coordinates the mixed fleet of container and pallet AGVs within shared traffic areas via the VDA 5050 interface. Previously, such innovation was reserved for the large AGV fleets of automotive OEMs. This solution now provides a compelling example of how industrial truck fleets can be effectively deployed in companies with only a few hundred employees. Especially in Germany, where SMEs form the backbone of the economy, this system has a very strong market relevance.
Functionality / Type of implementation |
++ |
Novelty / Innovation |
+ |
Customer benefit |
++ |
Market relevance |
++ |
++ very good / + good / Ø balanced / - less / -- not available |