IFOY Schirmherrschaft
IFOY Träger
IFOY Partner
Erweiterung des Automatiklagers Hase Safety Gloves GmbH
STILL
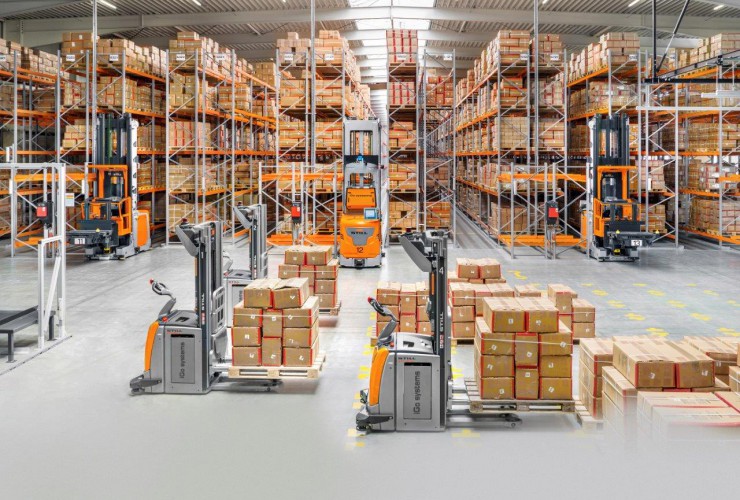
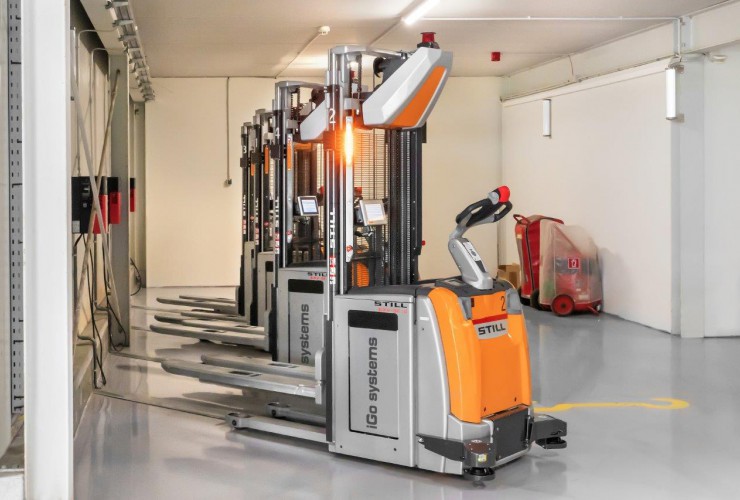
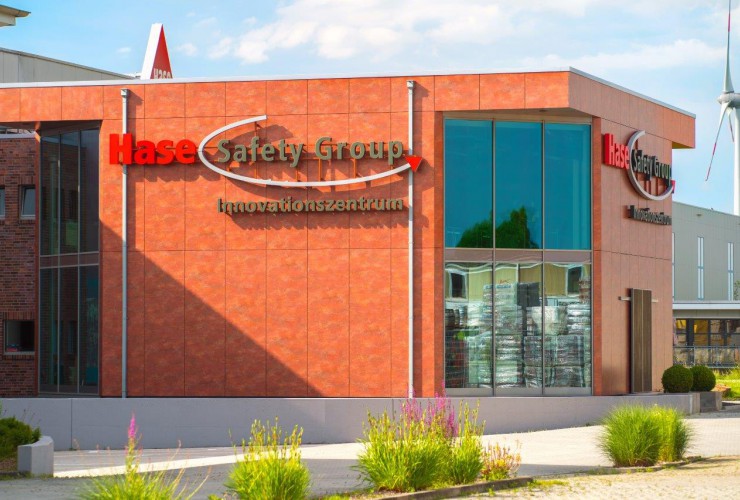
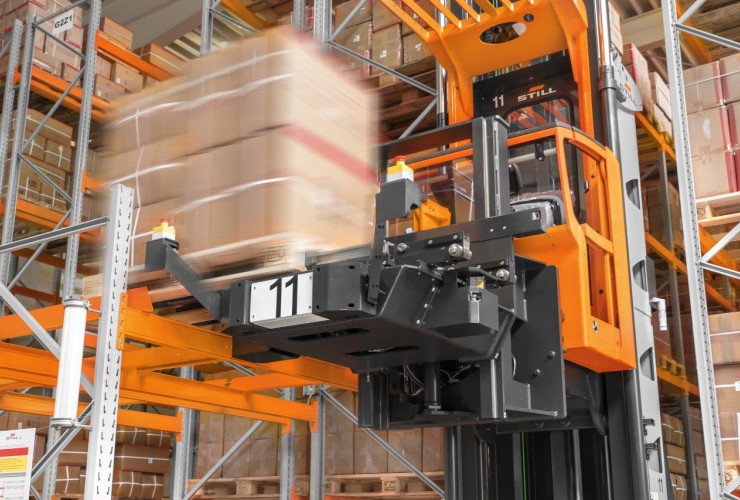
IFOY-Kategorie
Integrated Warehouse Solution
Zusammenfassung
STILL erweiterte die Regalanlage des Automatiklagers von Hase Safety Gloves auf insgesamt 10.000 Palettenstellplätze. Zugleich wurden die Flurförderzeuge von STILL durch neue, automatisierte und leistungsfähigere Geräte mit Teleskopgabeln ersetzt. Auch eine variable Warenübergabe ist mit den automatisierten Flurförderzeugen möglich. Von STILL optimierte und neu programmierte Fahrkurse tragen ebenfalls zur Steigerung der Performance bei.
Kunde
Hase Safety Gloves GmbH
Umsetzungszeitraum
Von: 31.05.2021
Bis: 30.10.2021
Investitionsvolumen
-
Bewerbungsdaten
Case Study
Mehr als 70 Jahren bildet die Herstellung von Arbeitshandschuhen das Kerngeschäft der Hase Safety Group AG im friesischen Jever. Bis heute steht der Kurs klar auf Wachstum. Darum wurde kürzlich ein Erweiterungsbau erstellt.
Die Aufgabenstellung lautete, eine höhere Lager- und Transporteffizienz zu erreichen. Eine besondere Herausforderung dabei stellte der Umbau im laufenden Betrieb dar. Dort sind neue Logistikflächen, ein Innovationszentrum mit Kundenschulungen, die Produktentwicklung und Produktdarstellung untergebracht. Theodor Wagner, Vorstand der Hase Safety Group AG, betont: „Nur so können wir den wachsenden Bedarf für neue Produkte decken. Mehr Warenumschlag für unser europaweites Kundengeschäft erfordert auch mehr Lagerkapazität sowie eine effiziente und wirtschaftliche Lagerhaltung.“
Höhere Produktivität durch mehr Automatisierung
Für kurze Wege sind die verschiedenen Artikel in Kartons verpackt und nach der ABC-Analyse übersichtlich und sortenrein auf Paletten im Schmalganglager eingelagert. Alle Automated Guided Vehicles (AGV) navigieren sicher und selbstständig dank rotierender Laserscanner, die fortwährend den Abstand zu den installierten Reflektoren messen. Drei MX-X Schmalgangstapler und sechs EXV-SF Hoch-Hubwagen der neuesten Generation wurden jeweils mit dem iGo Systems Automatisierungskit von STILL ausgestattet.
Beim Eingang eines Überseecontainers wird die kartonierte Ware per Teleskopförderband und Vakuum-Hebehilfe durch Hase-Mitarbeiter sortenrein palettiert und auf die Wareneingangsplätze verteilt. Maximilian Engels, Projektleiter und IT-Administrator von Hase Safety, erläutert: „Die Prozesse im Wareneingang haben wir weitgehend automatisiert. Durch manuelles Scannen, sowohl der Stellplätze als auch der Artikel, werden nun in unserem IT-System die automatisierten Einlagerungen ausgelöst.“
EXV Hoch-Hubwagen holen die fertigen Paletten ab und fahren sie durch die Konturenkontrolle. Dort wird gemessen, ob die Palette passende Maße aufweist oder etwa zu lang, zu breit oder zu hoch ist. Nach der Prüfung fährt ein EXV die Palette zum Übergaberegal im Schmalganglager. Dort wird sie von einem der automatisierten MX-X Hochregalstapler abgeholt und im zugewiesenen Stellplatz eingelagert.
Bei einer Auslagerung transportiert umgekehrt ein MX-X die entsprechende Palette zum Übergabeplatz. Diese wird wiederum vom EXV abgeholt und entweder zum Übergaberegal des manuellen Kommissionierlagers oder direkt zu den Versandspuren der Lkw transportiert. Sind die Ein- bzw. Auslagerungen erledigt, fahren die AGV automatisch in ihre Wartepositionen. Alle MX-X sind mit Teleskopgabeln ausgerüstet, da die Gassen bei Hase Safety deutlich schmäler sind und sich für Hochregalstaplern mit Schwenkschubgabeln nicht anbieten.
Im Vergleich zu einem Einsatz von Hochregalstaplern mit Schwenkschubgabeln können die Gassen bei Hase Safety daher sehr viel schmaler sein. Dank der Teleskopgabeln konnten sowohl die Lagerdichte als auch die Lagerkapazität deutlich erhöht werden.
Durch identische Komponenten, Steuerungen und Schnittstellen werden die Stapler zu leistungsfähigen AGV. „Eine Folge der Fahrkursoptimierungen ist eine geringere Anzahl an Transportaufträgen und damit verbunden weniger Bewegung der AGV. Dadurch hat sich auch die Sicherheit im Lager deutlich verbessert. Durch die enge Zusammenarbeit unseres Teams mit den Projektverantwortlichen von STILL konnten wir trotz der Corona-Pandemie die Software und die Hardware unseres Automatiklagers erfolgreich reorganisieren. Für zukünftige Herausforderungen sind wir also bestens gewappnet“, betont Maximilian Engels.
Autonomes Aufladen der Fahrzeugbatterien
Die moderne Photovoltaikanlage auf der über 10.000 Quadratmeter großen Dachfläche liefert grünen Strom zum Aufladen der Staplerbatterien. Lars Lemke, Projektleiter der STILL Niederlassung Bremen, hebt hervor: „Zum Laden der Batterien fahren die AGV selbstständig zu ihren Ladestationen. Ohne ein Kabel anschließen zu müssen, erfolgt die Aufladung der Batterie lediglich per Bodenkontakt. Dies ist ein weiteres Highlight: Denn jetzt können auch in der Nacht und ohne zusätzliches Personal die AGV ihre Batterien autonom aufladen.“
Ein-Schicht-Betrieb weiterhin möglich
Die Überseecontainer aus Bremerhaven werden nicht nur tagsüber, sondern auch am Abend angeliefert. Der erfahrene Unternehmer Theodor Wagner verdeutlicht: „Mit der Reorganisation unseres Automatiklagers können wir nun auch ohne Personalbedarf in den Abendstunden bzw. über Nacht die Einlagerungen automatisiert vornehmen. Dies ist ein wichtiger Anspruch an die neuen Prozesse. Bei den stetig steigenden Anforderungen am Markt können wir mit der neuen Anlage so unseren Ein-Schicht-Betrieb weiterhin aufrechterhalten.“
Maximale Flexibilität im skalierbaren Automatiklager
Aufgrund der Skalierbarkeit des Automatiklagers kann bei größeren Kapazitätsanforderungen mit zusätzlichen AGVs schnell und flexibel reagiert werden. Für den künftigen Bedarf stehen nun insgesamt 10.000 Palettenstellplätze zur Verfügung. Dass die AGVs für besondere Lagerprozesse auch manuell bedienbar sind, unterstreicht die Flexibilität im Automatiklager.
Fazit
Für zukünftige Anforderungen ist das moderne Distributionszentrum mit dem iGo Automatiklager von STILL bestens gerüstet. Kundenwünsche und Anforderungen der Großkunden können erfüllt und die Produkte europaweit und zeitnah ausgeliefert werden. „Start der ersten Automatisierungswelle unserer Logistik war bereits 2010. In den letzten Jahren haben wir unser Automatiklager stetig ausgebaut und im jüngsten Projekt auf den neuesten Stand gebracht. Seit über 30 Jahren haben wir dabei mit STILL einen zuverlässigen Partner an unserer Seite, der sehr schnell unsere Ideen in die Realität umsetzt“, fasst Theodor Wagner zusammen. Mit der bei Hase Safety Gloves umgesetzten Automatisierungslösung können auch viele andere Mittelstandsunternehmen ihre Logistikprozesse fit für die Zukunft machen – es zeigt sich einmal mehr, dass Automatisierung für jede Unternehmensgröße ein Thema ist.
IFOY Test
Name | STILL, Automatiklager-Erweiterung bei Hase Safety Gloves |
Category | Integrated Warehouse Solution |
Date of Test | 17.-23. März 2022 |
Testbericht
Hase Safety Gloves hat mithilfe von Still die Regalanlage seines Automatiklagers erweitert und die Prozesse effizienter gemacht – im laufenden Betrieb. Durch die Automatisierung der Anlage wurden zwar vier bis fünf Arbeitsplätze ersetzt, gleichzeitig hat man aber durch die Lagervergrößerung um 200 Prozent 15 neue Arbeitsplätze geschaffen.
80 Mitarbeitende, davon 70 am Hauptsitz in Jever, kümmern sich bei Hase Safety Gloves um ein- und ausgehende Arbeitssicherheitskleidung, die vorwiegend per Container aus Fernost kommt. Von den 12.000 Quadratmetern Lagerfläche bei Hase sind inzwischen alleine rund 7.000 Quadratmeter automatisiert, von den insgesamt 13.000 Stellplätzen im Lager können knapp 7.000 Stellplätze der Automatisierung zugerechnet werden. Mit einer 10.000 Quadratmeter umfassenden Photovoltaikanlage auf dem Dach werden zudem die im Lager eingesetzten Gabelstapler aufgeladen. Apropos Gabelstapler: Bei Hase wird erfolgreich nach dem „Mixed-Operations"-Betrieb gearbeitet: Stapler und Personal können sich begegnen, man hat bewusst auf den Einsatz von Schutzzäunen verzichtet.
Wenn Mitarbeiter nach dem Wareneingang eine gefüllte Palette auf einen Platz in der Bereitstellungsbahn setzen, bedeutet das gleichzeitig einen Fahrauftrag für ein Still-Gerät – es geht ab ins Lager oder Cross-Docking direkt weiter zum Warenausgang. Bei Hase gibt es automatische Ganzauslagerungen, aber auch manuelles Order-Picking. Bis es so weit ist, durchläuft die Palette vorher einen sogenannten Konturen-Check: ein Tor mit einem Laser-Vorhang, der Toleranzen der Palette eliminiert, damit das Automatiklager keinen „Bremsklotz" einlagert – denn sonst steht die Anlage. Wird ein Fehler festgestellt, wird die Palette sofort zum Nicht-in-Ordnung-(NiO-)Platz weitergereicht und das Problem beseitigt. Zum Einsatz kommen bei Hase drei automatisierte MX-X-Schmalgangstapler und sechs EXV-SF-Hochhubwagen der neuesten Generation, die alle mit dem iGo-Systems-Automatisierungs-Kit von Still ausgerüstet sind. Die EXV holen die sortenrein palettierte Ware am Wareneingangsplatz ab und bringen sie zum Übergaberegal im Schmalganglager, wo sie von einem der automatisierten MX-X-Geräte abgeholt und im zugewiesenen Stellplatz eingelagert wird. Beim Auslagern geschieht dieser Prozess in umgekehrter Reihenfolge. Haben die AGVs ihre Arbeit verrichtet, fahren sie automatisch in ihre Warteposition.
Ein Novum für Hase: Ein Wechselgang in der Mitte der Anlage, der zusammen mit einer Sprühnebelwand die sonst notwendige Brandschutzwand ersetzt, ermöglicht es den Gabelstaplern gleichzeitig, von einem Regalgang in einen anderen zu fahren, ohne an den Anfang des Regals zurückkehren zu müssen. Dabei fahren die Stapler im manuellen Bereich grundsätzlich im Ein-Schicht-Betrieb. Über Nacht wird dann nach dem „Opportunity-Charging"-Prinzip autonom aufgeladen, und zwar Blei-Säure-Batterien, die in dieser Anwendung wirtschaftlicher sind als Lithium-Ionen-Akkus. Die Regalgassen bei Hase können viel schmaler sein als normalerweise üblich: Im Vergleich zum Einsatz von Hochregalstaplern mit Schwenkschubgabel brauchen die mit einer Teleskopgabel ausgerüsteten MX-X deutlich weniger Platz, was sich vorteilhaft auf Lagerdichte und Lagerkapazität auswirkt.
Weil die Überseecontainer aus Bremerhaven nicht nur tagsüber, sondern auch am Abend angeliefert werden, ist es für Hase von Vorteil, dass mit der Reorganisation des Automatiklagers jetzt auch ohne Personalbedarf in den Abendstunden beziehungsweise in der Nacht Ware automatisch eingelagert werden kann. So kann der bestehende Ein-Schicht-Betrieb weiterhin aufrechterhalten werden.
IFOY Testfazit
Still hat Hase mit seiner Automatisierungslösung auf den neuesten Stand der Technik gebracht und zukunftsfähig gemacht. Mit der bei Hase umgesetzten iGo-Automatiklager-Lösung können auch andere Mittelständler ihre Prozesse verschlanken und auf den neuesten Stand bringen. Automatisierung, und das hat Still eindrucksvoll unter Beweis gestellt, ist ein Thema für (beinahe) jede Unternehmensgröße.
IFOY Innovation Check
IFOY Innovation Check
Marktrelevanz
Die Erweiterung bestehender Logistikstandorte ist ein häufig in der Praxis auftretender Fall. Die Veränderung der eigenen Produkte oder Produktionsabläufe, aber vielleicht noch mehr das geänderte Verhalten der Kunden mit dem Fokus auf Produktverfügbarkeit und kurzfristige Belieferung machen häufig Änderungen erforderlich. Von Änderungen betroffen können dann sowohl der Aufbau als auch die Abläufe sein. Das Beispiel bei der Firma Hase zeigt einen besonderen Fall auf, da die Möglichkeiten der Anpassungen im Layout sehr stark durch die verfügbare Grundfläche für Erweiterungen eingeschränkt waren. Außerdem hat der Eigentümer den unbedingten Willen zur Automatisierung an erste Stelle gebracht, wohingegen die Wirtschaftlichkeit einer Anwendung bei den meisten Anwendern die höchste Priorität einnimmt. Aus genannten Gründen ist die Marktrelevanz deshalb als gut zu bewerten, da die Lösung nicht uneingeschränkt auf die meisten Erweiterungsfälle übertragbar ist.
Kundennutzen
Gemessen an den eigenen Zielen hat der Kunde Hase sicher seine Ziele im hohen Maße erreicht. Mit Blick auf den allgemeinen Fall resultiert aus den zuvor genannten Gründen aber eine Beschränkung auf einen guten Kundennutzen.
Neuheitsgrad
Die spezifische Erweiterung des Lagers bei der Firma Hase ist gut gelöst und die Umsetzung mit hochmodernen Fahrzeugen auch auf aktueller Höhe der verfügbaren Technologien. Die Innovation resultiert aus der sachgerechten Kombination der bekanntermaßen gut funktionierenden Gewerke in einem sehr stark limitierten Umfeld. Ähnliche Lösungen konnten aber bereits vorher mit verfügbaren Geräten erzielt werden.
Funktionalität / Art der Umsetzung
Die vielfältigen Einschränkungen der Erweiterung im Bestand wurden bei der Realisierung der Lösung gut berücksichtigt. Die Lösung bietet viele Funktionen für den Betreiber und stellt ihm alternative Nutzungsmöglichkeiten der Fahrzeuge als Redundanz oder zum Abfangen von Leistungsspitzen zur Verfügung.
Fazit
Die Erweiterung im Bestand ist beeindruckend und die Umsetzung mit hochmodernen Fahrzeugen gut gelöst. Die Innovation resultiert aus der guten Kombination der bekanntermaßen gut funktionierenden Gewerke in einem sehr stark limitierten Umfeld.
Marktrelevanz |
+ |
Kundennutzen |
+ |
Neuheitsgrad |
Ø |
Funktionalität / Art der Umsetzung |
+ |
++ sehr gut / + gut / Ø ausgeglichen / - weniger / - - nicht vorhanden |
Extension of the automated warehouse of Hase Safety Gloves GmbH
STILL
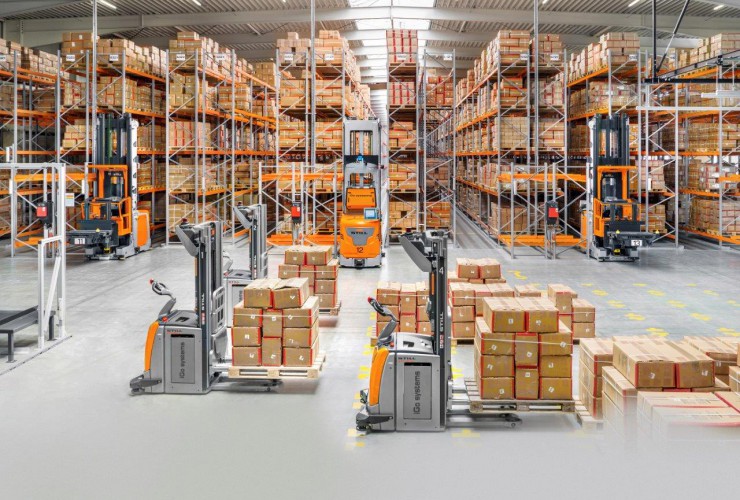
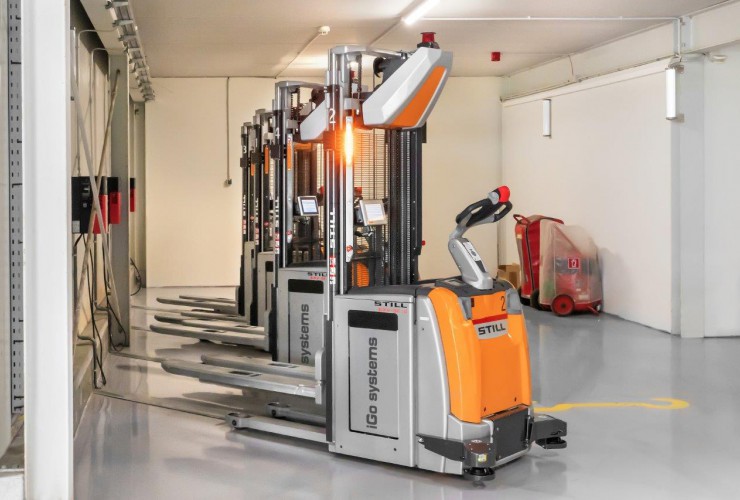
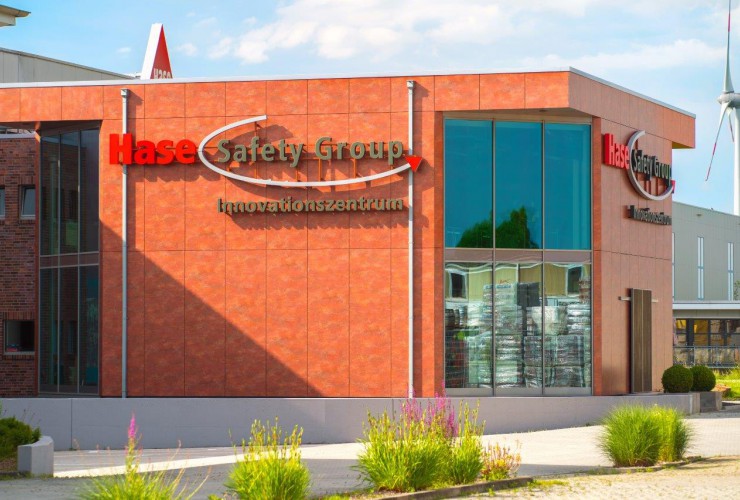
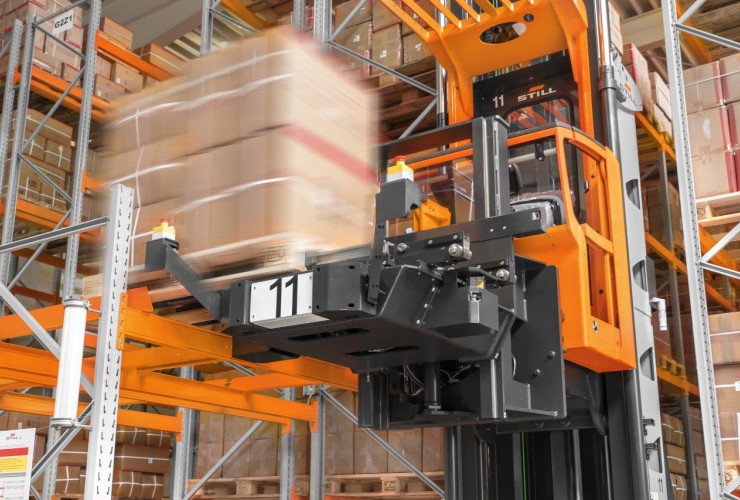
IFOY category
Integrated Warehouse Solution
Summary
Hase Safety Group sets course for growth: Automated industrial trucks are also very flexible in combination with variable goods transfer. One example is the expansion of the automated warehouse at Hase Safety Gloves GmbH. There, the STILL industrial trucks were replaced by new automated, more powerful vehicles with telescopic forks. Newly programmed route optimisations also contribute to the increase in performance. STILL expanded the racking system to a total of 10,000 pallet spaces.
Customer
Hase Safety Gloves GmbH
Realisation Phase
From: 2021-05-31
To: 2021-10-30
Investment
-
Entry Data
Case Study
For more than 70 years, the production of work gloves has been the core business of Hase Safety Group AG in the Frisian town of Jever. In 2013, the German company celebrated 75 years of company history. Due to the growth of the Hase Safety Group, the existing space and handling capacities were no longer sufficient. The task was therefore to achieve greater storage and transport efficiency. One particular challenge was the conversion during ongoing operations. Until today, the course is clearly set on growth. That is why an extension was recently built. It houses new logistics areas, an innovation centre for customer training, product development and product presentation. Theodor Wagner, CEO of Hase Safety Group AG, emphasises: "This is the only way we can meet the growing demand for new products. More turnover of goods for our Europe-wide customer business also requires more storage capacity as well as efficient and economical warehousing."
More productivity through more automation
To keep distances short, the various glove articles are packed in cartons and stored neatly by type on pallets in the narrow-aisle warehouse according to the ABC analysis. For safe and independent movement of the vehicles, all AGVs (Automated Guided Vehicles) navigate with rotating laser scanners that constantly measure the distances to the installed reflectors. Three MX-X very narrow aisle trucks and six EXV-SF high lift stackers of the latest generation were each equipped with STILL's iGo Systems automation kit.
At the goods receipt of an overseas container, the cartons with new goods are palletised by Hase employees using a telescopic conveyor belt and a vacuum lifting aid and distributed to the goods receipt locations according to type. Maximilian Engels, project manager and IT administrator at Hase Safety, explains: "We largely automated the processes in the goods receiving area. By manually scanning the storage locations as well as the articles, the automated storage processes are now triggered in our IT system."
EXV high lift stackers pick up the finished pallets and drive them through the contour check. There, the pallet is measured to see if it is too long, too wide or too high. If successful, an EXV moves the pallet to the transfer rack in the narrow-aisle warehouse. There it is picked up by one of the automated MX-X high-bay stackers and stored in the assigned storage location.
In the case of a retrieval, an MX-X transports the respective pallet to the transfer station. The pallet is then picked up by the EXV and transported either to the transfer rack of the manual picking warehouse or directly to the shipping lanes of the trucks. Once the storage and retrieval operations have been completed, the AGVs automatically move to their waiting positions. All MX-X are equipped with telescopic forks, as the aisles at Hase are significantly narrower and thus not suitable for high bay stackers with swivel traverse forks. By using telescopic forks, both the storage density and the storage capacity are higher.
Identical components, controls and interfaces turn the trucks into high-performance AGVs. "One effect of the route optimisations is a lower number of transport orders and, as a result, less movement of the AGVs. This has also significantly improved safety in the warehouse. Thanks to the close cooperation between our team and the STILL project managers, we were able to successfully reorganise both the software and the hardware of our automated warehouse despite the Corona pandemic. Now we are well prepared for the challenges that lie ahead in the near future," emphasises Maximilian Engels.
Autonomous charging of the vehicle batteries
The state-of-the-art photovoltaic system on the more than 10,000 quare metre-sized roof supplies green electricity to charge the forklift batteries. Lars Lemke, project manager from STILL's Bremen branch points out: "To charge the batteries, the AGVs move to their charging stations independently. Without having to connect a cable, the battery is charged simply by contact with the ground. This is another highlight: because now the AGVs can charge their batteries autonomously at night and without additional personnel."
One-shift operation still possible
The overseas containers from Bremerhaven are not only delivered during the day, but also in the evening. The experienced entrepreneur Theodor Wagner clarifies: "With the reorganisation of our automated warehouse, we can now also carry out automated storage in the evenings or overnight without the need for staff. This is an important requirement for the new processes. Even with constantly increasing demands on the market, we can continue to maintain our one-shift operation with the new system."
Maximum flexibility in the scalable automated warehouse
Due to the scalability of the automated warehouse, it is possible to react quickly and flexibly to larger capacity requirements with additional AGVs. For the demand in the near future, a total of 10,000 pallet storage locations are now available.
The fact that the AGVs can also be operated manually for special storage processes underlines the flexibility of the automated warehouse.
Summary
With the iGo automated warehouse from STILL, the modern distribution centre is ideally equipped to meet the future requirements, including those of other medium-sized companies. Customer requests and the requirements of major customers are thus fulfilled and the products are delivered across Europe, promptly and in a timely manner. "The first wave of logistics automation started back in 2010, and in recent years we have steadily expanded our automated warehouse and brought it up to date with the latest project. For more than 30 years, we have had a reliable partner at our side in STILL, who very quickly turns our ideas into reality," summarises Theodor Wagner. Once again it shows that automation is an issue for companies of all sizes and has now finally arrived in the SME sector too.
IFOY Test
Name | STILL, Automated warehouse extension at Hase Safety Gloves |
Category | Integrated Warehouse Solution |
Date of Test | March 18 to March 23, 2022 |
Test Report
With the help of Still, Hase Safety Gloves has expanded the system of its automated warehouse and made the processes more efficient - during ongoing operations. Although four to five jobs were replaced by automating the system, 15 new jobs were created at the same time by expanding the warehouse by 200 per cent.
80 employees, 70 of them at the headquarters in Jever, take care of incoming and outgoing work safety clothing at Hase Safety Gloves, which mainly arrives by container from the Far East. Of the 12,000 square metres of warehouse space at Hase, around 7,000 square metres alone are now automated, and of the total 13,000 storage spaces in the warehouse, just under 7,000 spaces can be attributed to automation. A 10,000 square metre photovoltaic system on the roof is also used to charge the forklifts used in the warehouse. Speaking of forklifts: Hase successfully operates according to the "mixed operations" principle: Forklifts and staff can meet each other, and the use of protective fences has been deliberately dispensed with.
When employees place a filled pallet on a place in the staging lane after goods receipt, this simultaneously means a transport order for a still unit - it goes off to the warehouse or cross-docking directly to goods issue. At Hase, there is automatic whole stock removal, but also manual order picking. Until this happens, the pallet first goes through a so-called contour check: a gate with a laser curtain that eliminates tolerances of the pallet so that the automatic warehouse does not store a "brake block" - otherwise the system stops. If an error is detected, the pallet is immediately forwarded to the "not right" location and the problem is eliminated. Hase uses three automated MX-X narrow-aisle stackers and six EXV-SF high-lift trucks of the latest generation, all of which are equipped with Still's iGo Systems automation kit. The EXVs pick up the sorted palletised goods at the goods-in location and take them to the transfer rack in the narrow-aisle warehouse, where they are picked up by one of the automated MX-X units and stored in the assigned bin location. For retrieval, this process happens in reverse order. Once the AGVs have done their work, they automatically move to their waiting position.
A novelty for Hase: a changeover aisle in the middle of the system, which, together with a spray wall, replaces the otherwise necessary firewall, enables the forklifts to move simultaneously from one racking aisle to another without having to return to the beginning of the racking. In the manual area, the forklifts always run in single-shift operation. Overnight, they are then autonomously recharged according to the "opportunity charging" principle, using lead-acid batteries, which are more economical than lithium-ion batteries in this application. The racking aisles at Hase can be much narrower than is normally the case: compared to the use of high-rack forklifts with swivel reach forks, the MX-Xs equipped with telescopic forks require significantly less space, which has a beneficial effect on storage density and capacity.
Because the overseas containers from Bremerhaven are not only delivered during the day, but also in the evening, it is an advantage for Hase that with the reorganisation of the automatic warehouse, goods can now be stored automatically in the evening hours or at night without the need for personnel. This means that the existing single-shift operation can continue to be maintained.
IFOY Test Verdict
With its automation solution, Still has brought Hase up to the state of the art and made it fit for the future. With the iGo automated warehouse solution implemented at Hase, other medium-sized companies can also streamline their processes and bring them up to date. Automation, and this has been impressively demonstrated by Still, is a topic for (almost) any size of company.
IFOY Innovation Check
IFOY Innovation Check
Market Relevance
The expansion of existing warehouse locations is a frequent case in practice. Changes in the company's own products or production processes, but perhaps even more so the changed behaviour of customers with a focus on product availability and short-term delivery, often make changes necessary. Both the structure and the processes can be affected by changes. The example at the Hase company shows a special case, as the possibilities for adjustments in the layout were very much limited by the available floor space for extensions. In addition, the owner put the unconditional will to automate first, whereas the economic efficiency of an application is the highest priority for most users. For the above reasons, the market relevance can therefore be rated as good, as the solution cannot be transferred to most extension cases without restrictions.
Customer Benefit
Measured against its own objectives, the customer Hase has certainly achieved its goals to a high degree. With regard to the general case, however, a limitation to a good customer benefit results from the previously mentioned reasons.
Novelty
The specific expansion of the warehouse at Hase is well solved and the implementation with state-of-the-art vehicles is also at the current level of available technologies. The innovation results from the appropriate combination of the known well-functioning trades in a very limited environment. However, similar solutions could be achieved before with available equipment.
Functionality / Type of Implementation
The many limitations of the extension in the existing building were well taken into account in the realisation of the solution. The solution offers many functions for the operator and provides him with alternative uses of the vehicles as redundancy or to absorb power peaks.
Verdict
The expansion in the existing stock is impressive and the implementation with state-of-the-art vehicles is well solved. The innovation results from the good combination of the known well-functioning trades in a very limited environment.
Market Relevance |
+ |
Customer Benefit |
+ |
Novelty |
Ø |
Functionality / Type of Implementation |
+ |
++ very good / + good / Ø balanced / - less / - - not available |